Behind the Scenes at NAB - An Industry Expert Perspective
When executing a trade show booth for a client at the annual National Association of Broadcasters (NAB) Show, layers upon layers of essential experts and processes intertwine and work in harmony to execute the splendor of an ASTOUND exhibit.
The logistics are orchestrated by our talented team of designers, account and project managers, operations managers, shop staff, and install and dismantle crew. The multitude of challenges and solutions that need to be addressed is large, but when the chain of processes is streamlined, execution can appear effortless.
Located at the Las Vegas Convention Center (LVCC), clients at NAB have the benefit of being in close proximity to ASTOUND’s Vegas-based production facilities and offices. This convenience allows our on-site teams to take full advantage of our nearby staff and resources to seamlessly address any logistical challenges and adapt our approach to unforeseen hurdles, with little lead time.
Our logistical consideration starts at the very beginning - in the design phase. Drayage costs and the total weight of an exhibit are highly correlated, so as a general practice, careful material selection is an important part of how we approach design, aesthetically and functionally. The broadcast industry is predominately about delivering video content, a de-materialized product which follows the same design philosophy by which we approach booth design for this industry; the design aim is always to produce the most lightweight modules to maximize cost efficiency.
On the other hand, the broadcast industry is also about the back-end equipment that delivers content, which often requires some bulk in tech rooms and engine rooms. For projects with this type of requirement, we design to float engine and tech rooms into the walls.
Good, clear communication is necessary between all departments to align all these pieces cohesively. When we start at the design and solution and estimating stage, we consider alternate materials and lightweight solutions to guarantee the final product is built as efficiently as possible to ensure cost reductions down the line in all respects.
For instance, the effective use of materials and thoughtful weight management affects how our trucks are packed for shipping. Larger and heavier components would require additional transport, upping trucking costs as we distribute weight safely to accommodate for them. It would also require more fuel, and we always strive to minimize our environmental footprint as much as possible.
With drayage costs, not only do we have to consider our internal shipping requirements, it is also imperative to be aware of what and how we are receiving shipments from external vendors. We must know the different types of packaging - crates, containers, pallets, etc. and how they’re being shipped -FedEx, UPS – to plan accordingly. Is it a last minute shipment that could cost extra? Were we expecting a box and was sent a pallet? Knowing advanced details such as if the client needs products or models that required being shipped in a certain time frame all play into the bottom line as we organize our transport to the LVCC. If we anticipate we’re expecting x number of packages, but then receive x + 1, that again could require the use of an additional truck, tacking on additional costs.
Foreseeing the number of trucks needed gives our team an accurate picture of trucking costs upfront. At the same time, making the most of our preferred carriers ensures the rates we receive are the most economical and competitive.
Working a broadcast-focused convention brings its own set of unique challenges that have to be circumvented for the booth to be called a success. Being rather AV heavy, the project scope is slightly different from other shows.
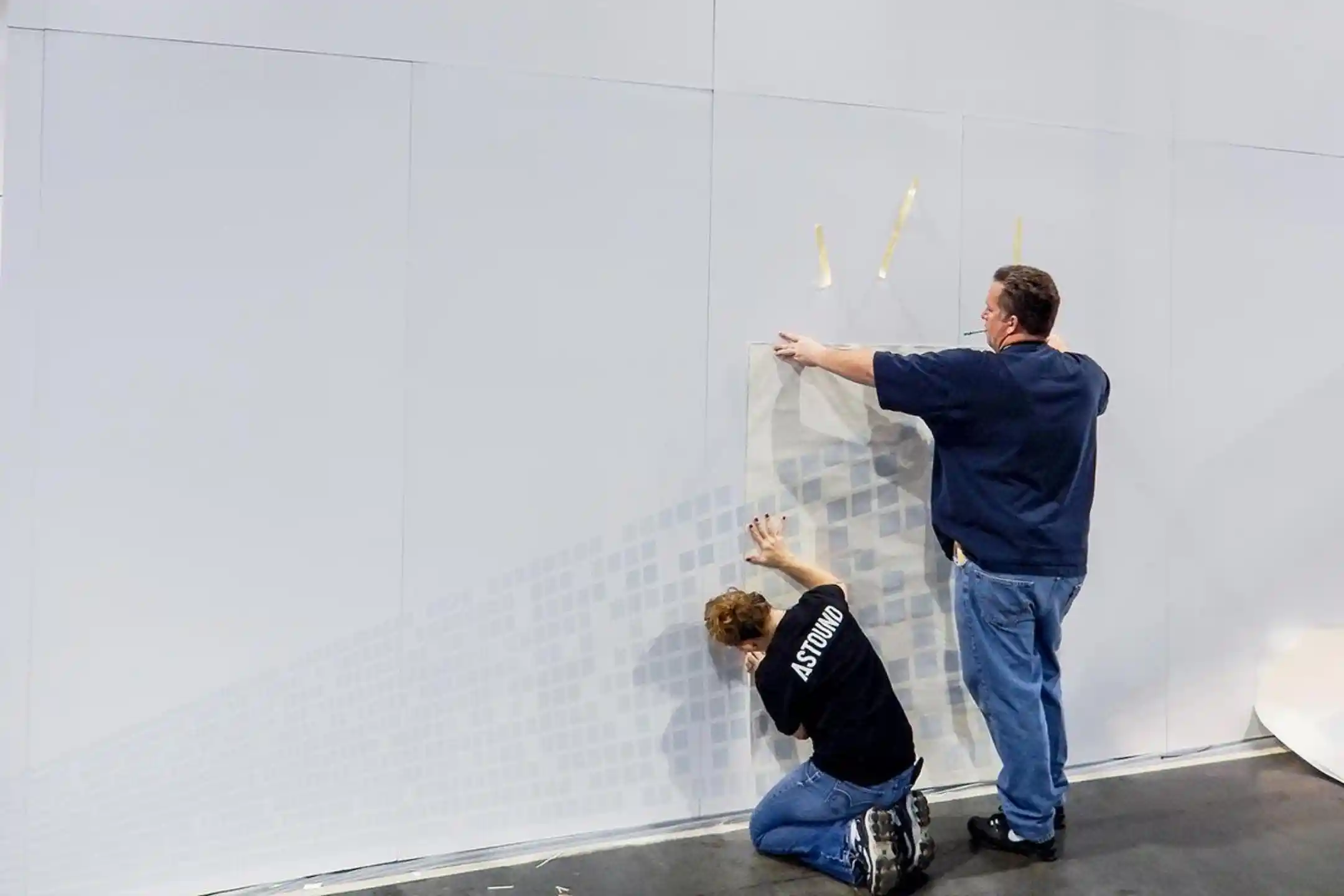
In particular, cable management is an essential component to a well-thought-out booth. This is an element that is sometimes easy to overlook during the actual production of the job since design renderings tend to omit this detail. As a result, during our review stage, we resolve these areas by going over our renderings to strategize wiring and electrical details. If we have a design with a large number of LED screens for example, integrating the wires so the design looks clean is vital in the thought process.
Unconsidered AV gaps run the risk of leaving bundles of wires exposed and looking unprofessional and messy. Certain ‘gravity defying’ booths also need to be carefully planned. While we work hard to camouflage wires, they still need to be easily accessible. These considerations make our exhibits appear smarter and sharper on the show floor and our teams take pride in those small but crucial details.
These factors play a significant role in why clients trust us at NAB – our team plans smart. Not only that, we watch over the entire procedure from start to finish. Our eye on the project allows us to manage multiple clients at the show with ease. We do that by ensuring our key players are out there as support systems on-site–our command center otherwise known as our project managers and our site supervisors. Our presence is always known. When you have an ASTOUND booth at the LVCC, staff is not only there on-site, but a vast base of on-call support is also available as needed.
Our work during the show relies heavily on the ASTOUND site supervisor. He is the captain of the ship, the one who has the show package, every direction and the list of items. He establishes the starting point with the open first crate to launch set-up. As a result, the team is able to set up the properties in order from there, in a coherent rhythm, making sure pieces are not lying on the floor in the way, as assembly is coordinated.
Our method of starting right from the design phase straight through to the end result on the show floor provides a level of comfort we want to afford all our clients at NAB. Knowing our clients see our efficiency and how our team organizes from top to bottom, leaves no question in their mind that their booth is going to be a show stopper by the time its finished.
From more on how ASTOUND can help you behind the scenes, please contact us.